Table Of Content
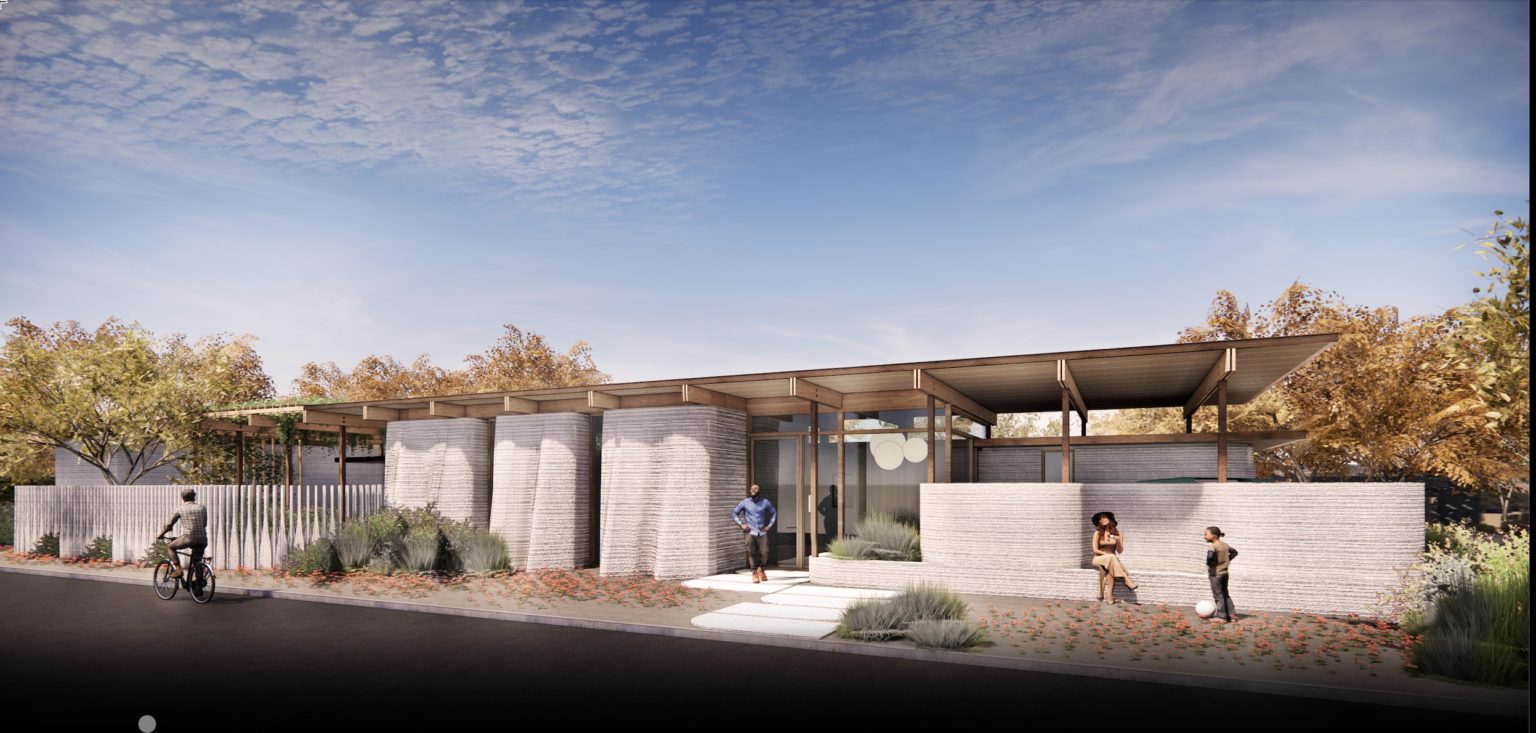
One of the most time-consuming tasks in building a house is the construction of walls. With 3D printing through an autonomous robotic construction system, you can save large amounts of time and build a house in weeks or days instead of months. The time savings directly translate to savings in the overall cost of the house. Initial printing speeds of 20 pounds per hour have since ramped up to nearly 500 pounds per hour, significantly reducing construction costs. This efficiency, combined with local materials, makes the process more sustainable and resilient to global supply chain disruptions.
Branch Technology C-FAB and WATG’s Curve Appeal design
Another of ICON’s recent undertakings includes the construction of the largest 3D printed house community in Texas. It plans on 3D printing around 100 houses in the neighborhood of Austin, Texas. These are some of the promising projects in the US if you’re planning on buying a 3D printed home for yourself. Currently, 3D printed houses are still in their nascent stages, and few projects are available commercially. The Alquist’s Project Virginia and the SQ4D’s home are excellent examples of projects ready to buy in the US. 3D printed homes are made using concrete, one of the most durable and long-lasting materials available.
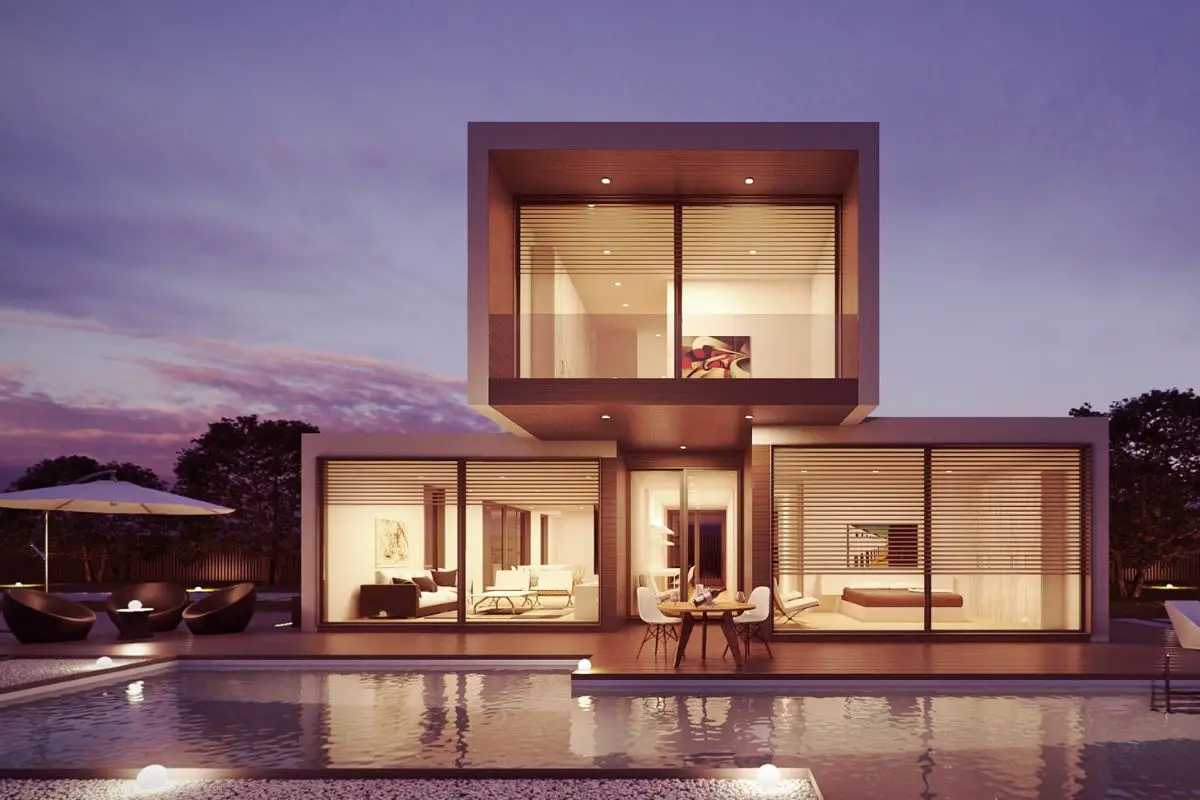
Best DIY 3D Printer Kits in 2024 (From $150!)
ICON was the first company in the United States to get a permit to build a fully 3D printed house back in 2018. This house was constructed in collaboration with New Story in Austin, Texas, and was meant to demonstrate the practicality of 3D printing in the construction industry. Some brand new 3D printed houses can cost almost as half as a traditional one, and they are becoming more and more popular as the technology improves.
Tools Needed To Build A 3D Tiny House
In June 2022, the National Association of Home Builders brought forward the idea of developing a separate building code category for 3D printed housing regulations, but this is still in the works. While it’s highly likely that houses like this may develop their own laws in the future, they’re under general laws for now. After the instructional code is set, the 3D printer will then do exactly what it’s told and manufacture the foundation and outer walls of the house, layer by layer. The process looks kind of like a giant tube of toothpaste squeezing out line after line of wet concrete. 3D printing can significantly reduce the amount of waste generated during the construction process. Additionally, 3D printing can use sustainable materials, such as recycled plastic, which can reduce the environmental impact of construction.
Quality and Durability of 3D Printed Houses
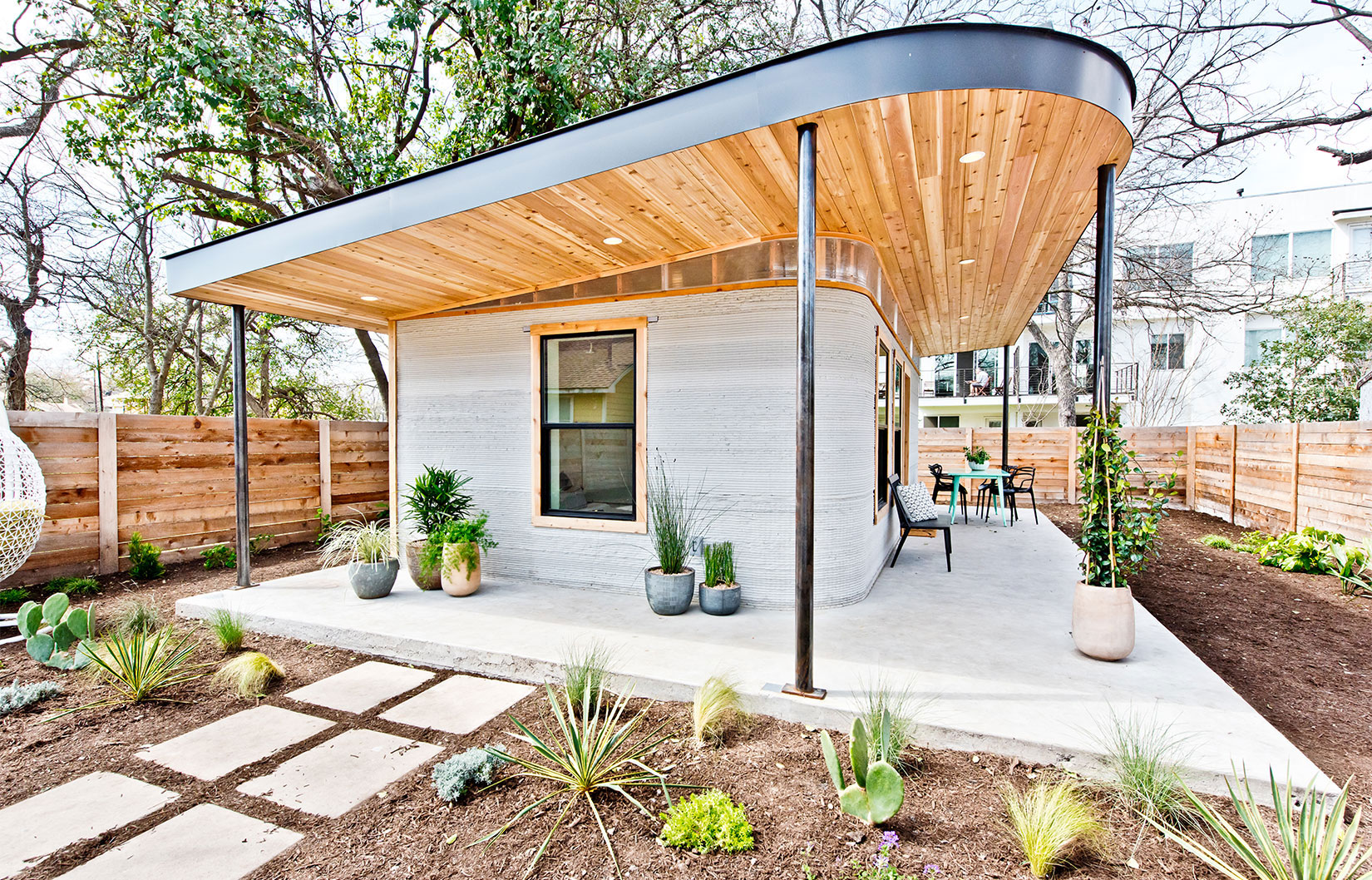
Just as with traditionally constructed homes, 3D-printed homes are available at a variety of price points — though they are generally more affordable. “3D homes will definitely have a large impact on the real estate industry because of two important reasons,” said Theresa Raymond, broker and owner at TN Smoky Mtn Realty. 3D homes are unimaginably cheaper to construct, and it’s possible to build a complete house in 24 hours. 3D printed homes also have the potential to be disaster-resistant which is an essential factor to consider when building in regions that are prone to natural disasters. With the continuously decreasing number of skilled laborers available, it is becoming increasingly difficult to source good quality labor for building constructions. Add to that the continuously increasing labor costs, and it is no surprise that housing prices have increased astronomically in recent years.
Best 3D Printers in 2024 (All Budgets)
SQ4D has used its proprietary Autonomous Robotic Construction System (ACRS) for building the house. Using the ACRS, the house was built in under 48 hours and required at most three people to monitor and run the machine. The Tvasta house was built on IIT Madras’ campus ground and covers approximately 600 sq ft. (55.74 m2) of floor space. It was constructed off-site using Tvasta’s concrete 3D printer and comprised several sections. All the units were later brought on site and assembled to form a two-bedroom house with a hall and kitchen. However, this is America, so it’s not like people built this thing just to help the unhoused.
Icon 3D-printed houses are leading a revolution in real estate - CBS News
Icon 3D-printed houses are leading a revolution in real estate.
Posted: Mon, 09 Oct 2023 07:00:00 GMT [source]
What are the disadvantages of houses built with 3D concrete printing?
The Sky's the Limit with New Multistory 3D Printed House Builder - All3DP
The Sky's the Limit with New Multistory 3D Printed House Builder.
Posted: Mon, 18 Mar 2024 07:00:00 GMT [source]
The building will contain 4,090 square feet of live-in space and hold five apartments and a basement. After the material extrusion is complete, a concrete dryer is attached to the industrial-grade printer that allows the concrete to solidify almost immediately so that another layer of material can be added to the build. Designers use embellishments likes shelves and room dividers to separate these rooms. When it comes to 3D printing a house, there are several factors that can affect the overall cost of the project. In this section, we will discuss the main factors that can impact the cost of 3D printing a house.
Indeed, since construction 3D printers reduce the need for manual labor, they create much less employment for local workers. Most 3D printed homes’ exteriors are not as smooth as traditionally-built houses. Like any technology innovator, Citizen Robotics is trying to create the chicken and the egg at the same time. 3D-printed homes won’t be affordable unless they’re widespread, and might not become widespread if they’re not affordable. In Youngstown, Pantheon Innovative Builders is partnering with Ohio State University to research 3D printing. And, in Columbus, Vitruvianis looking at bringing the concrete homes to Central Ohio.
Cleveland’s city council has even floated a proposal to buy a large-scale 3D printer for housing. All hope the technology can be a strong tool in creating more affordable housing across the state. The inaugural Havelar house, a collaboration with renowned architects Aires Mateus, Glória Cabral, and Francis Kéré, is a showcase of what is achievable with 3D construction printing technology. This process created a stronger and longer-lasting building material compared to traditional techniques, making the houses tougher in the face of extreme weather. Bologna-based architecture studio Mario Cucinella Architects and 3D-printing specialists WASP collaborated to create a 60-square meter low-carbon housing prototype named Tecla – a combination of the words technology and clay.
3D printing technology has revolutionized the construction industry, and it has the potential to significantly reduce the cost of building a house. 3D printing technology has revolutionized a wide range of industries, from automotive to healthcare to aerospace. One industry that has been particularly impacted by 3D printing is construction. 3D printed homes are becoming increasingly popular due to their potential to be built faster, cheaper, and with less waste than traditional construction methods. One of the most common questions people have about 3D printed homes is how much they cost. While the cost of a 3D printed home can vary depending on a variety of factors, including location, size, and design, they are generally less expensive than traditional homes.
The construction industry is highly regulated, and building codes vary from state to state and country to country. Currently, there is no clear regulatory framework for 3D printed houses, which makes it difficult for builders and developers to navigate the legal landscape. The complexity of the design is another factor that can affect the cost of a 3D printed house. A more complex design will require more time and effort to print, which can increase the overall cost of the project. Additionally, a more complex design may require more advanced printing technology, which can also add to the cost.
No comments:
Post a Comment